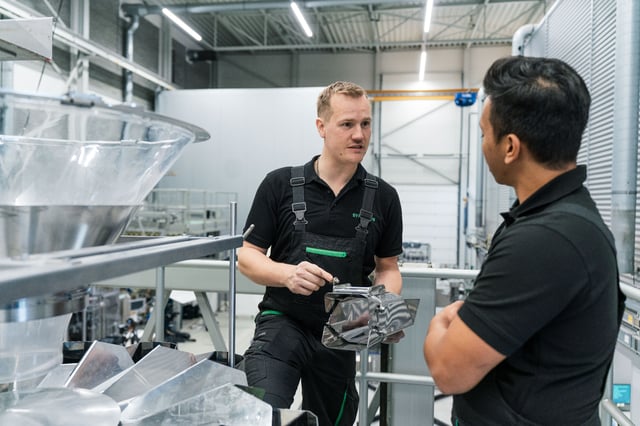
Service Agreements
サービスプログラムの詳細については、こちらをご覧ください。
Small and large volume parenteral drug product formulation
In drug product formulation, where the equipment functionality required is highly dependent on the drug product type, modularization is proving a decisive design advantage to help meet the need for both process flexibility and exceedingly short delivery times. Syntegon’s SVP and LVP modular solutions for batch sizes ranging from 13-20,000 liters are suitable for the GMP manufacture of small volume parenterals (SVP), large volume parenterals (LVP), infusion products (IV), as well as buffer and media preparations. We offer a full range of process vessels and their automation as well as all associated peripherals including media supply, CIP/SIP systems, and the filling line interface.
Our SVP/LVP process systems are highly modular and flexible solutions for the production of liquid pharmaceuticals. Where desirable, they feature a prefabricated integrated cleanroom design with all peripheral technology outside the cleanroom in technical skids. The production area itself can also be separated and run under different room classifications as required by the application. We provide the highest degree of flexibility in both the layout of your room concept and the configuration of the production units themselves.
Our industrial designers and engineers have developed the SVP/LVP process system in close cooperation with our customers with a clear common objective: achieving the greatest possible flexibility with maximal ease of operation. The result is a modular, highly flexible system. We use pre-tested functional modules to configure each customer’s individual solution. Syntegon and the customer jointly define the shape, volume, and functionality of the fixed or mobile containers, which allows us to deliver exactly the preparation system the customer needs for his products. Over 70 pre-tested functional modules are available to process batch sizes from 13 to 20,000 liters, offering unique versatility and convenience.
We offer multiple options for substance addition. You can feed APIs and excipients either manually or, when handling larger amounts or critical substances, through vacuum conveyors, liquid dosing stations, or containment solutions for sterile or toxic substances. A full range of dry and liquid materials alike can be seamlessly added to all the processing vessels. Regardless of the selected options, we deliver all solutions with an “out of the box” approach.
Solutions, suspensions, and emulsions alike, all require the right approach to mixing and homogenizing the preparation to provide the necessary product quality. The SVP/LVP offers a wide range of options including low and high shear mixers, high performance homogenizers and emulsifiers, as well as vibration mixers. Is bioburden reduction, sterile filtration, or aseptic processing required? Also not a problem with the SVP/LVP. Our integrated sterile filter stations come in a wide range of sizes, all optimized to minimize product loss.
Our automation architecture, which is structured according to ISA-88, is one of the foundations of our modularization concept. Mechanics, electronics, and software merge into intelligent mechatronic modules in our systems. Your individual recipes can be implemented in three different ways on the SVP/LVP process system: program, production, and batch management sequences. The result is unparalleled flexibility in production monitoring and control. We thrive defining trends and driving digital production in drug product formulation.
The Syntegon portfolio covers the entire liquid pharmaceutical manufacturing process, from pure media generation to final product packaging. Thanks to cutting-edge engineering, a high degree of digitalization, automation, and the continuous flow of data, you receive your entire project scope fully integrated from one source. And that also includes our formulation and filling solutions: our modular SVP/LVP process system truly is “the perfect match for every batch” – whether you purchase a stand-alone machine or an entire line.
In drug product formulation, where the equipment functionality required is highly dependent on the drug product type, modularization is proving a decisive design advantage in meeting the ever greater need for both process flexibility and short delivery times.
Our modular formulation system concept
Our formulation systems are fully standardized platforms based on off-the-shelf functional modules. Where desirable, they feature a prefabricated integrated cleanroom design with all peripheral technology outside the cleanroom in technical skids. The production area itself can also be separated, and run under different room classifications as required by the application. Our solutions provide the highest degree of flexibility in both the layout of your room concept and the configuration of the production units themselves. We jointly define the shape, volume, and functionality of the fixed and mobile containers to deliver exactly the preparation system you need for your products. Over 70 pre-tested functional modules are available to process batch sizes from 13 to 20,000 liters, offering unparalleled flexibility and convenience.
From mobile homogenizers to integrated CIP/SIP modules, a full range of options are available. For example, the prefabricated integrated cleanroom design can even include the laminar flow and lighting units. And since the safety of operators and products comes first, we can meet complex requirements such as aseptic processing or the handling of toxic substances simply by adding the appropriate functional modules.
Our automation architecture, which is structured according to ISA-88, is one of the foundations of our modularization concept. Mechanics, electronics, and software merge into intelligent mechatronic modules in our systems. Your individual recipes can be implemented in three different ways on the SVP/LVP process system: program, production, and batch management sequences. The result is unparalleled flexibility in production monitoring and control. We thrive defining trends and driving digital production in drug product formulation. The modularity of the Syntegon formulation platform, and the flexibility it provides, makes for a highly compelling solution for a full range of clinical to commercial liquid pharmaceutical product formulation applications. The system is, truly, “the perfect match for every batch."
The Syntegon formulation solutions provide everything you need for a highly flexible yet seamlessly integrated system infrastructure. We offer a full range of process vessels, their automation, as well as all associated peripherals including media supply, CIP/SIP systems, and the filling line interface.
Our SVP process system is a highly modular and flexible solution for the production of small volume parenterals (SVP). It features a prefabricated integrated cleanroom design with all peripheral technology outside the cleanroom in a technical skid. The production area itself can also be separated, and run under different room classifications, as required by the application. We provide the highest degree of flexibility in the layout of your room concept and in the configuration of the production units themselves.
The SVP Essential liquid formulation system is a new 1- or 2-vessel standardized variant of the highly versatile SVP platform. Ideally suited for simple aqueous solution and suspension parenteral products, the SVP Essential is designed for process flexibility with ultra-fast delivery. The customer receives the precise functionality required for the intended range of products in a drop-in configuration that can be rapidly delivered, installed, qualified, and put into operation. The SVP Essential has a clear value proposition: GMP process flexibility with unparalleled speed and convenience.
The LVP process system uses Syntegon standards to deliver highly customized solutions for the production of large volume parenterals (LVP), infusion products (IV), as well as buffer and media preparations. The liquid preparations are carried out in modular temperature-controlled stainless-steel tanks with all the appropriate functionality to cover the full range of your product recipes. All LVP solutions follow the applicable compendial (e.g. USP, EP) as well as regulatory (e.g. DIN, ASME, GMP, and FDA/EMA) pharmaceutical manufacturing guidelines.
Our CIP/SIP systems are designed for the purification and sterilization of pharmaceutical processing components, equipment, and systems. The internal or external CIP/SIP systems use PW, WFI, PS, and application-specific cleaning solutions with recirculation for the efficient use of the cleaning media. The smart system design guarantees simple self-purification with special dosage and heating/cooling systems providing a constant and consistent high purification quality.
The Syntegon portfolio covers the entire liquid pharmaceutical manufacturing process, from pure media generation to final product packaging. Thanks to cutting-edge engineering, a high degree of digitalization, automation, and the continuous flow of data, you receive your entire project scope fully integrated from one source. And that also includes our formulation and filling solutions: our modular SVP/LVP process system truly is “the perfect match for every batch” – whether you purchase a stand-alone machine or an entire line.
サービスプログラムの詳細については、こちらをご覧ください。
デジタルソリューションの詳細については、こちらをご覧ください。
スペアパーツの詳細については、こちらをご覧ください。
メンテナンスの詳細については、こちらをご覧ください。
リモートサービスの詳細については、こちらをご覧ください。
最新化(改造)の詳細については、こちらをご覧ください。
トレーニングの詳細については、こちらをご覧ください。
コンサルティング関連サービスの詳細については、こちらをご覧ください。
「持続可能性、効率性、デジタル化、安全性、柔軟性」は、産業における重要なトレンドです。 私たちは自社の技術やノウハウを活用して、これらの課題に対する解決策を開発し、未来の製造業を形作っています。